COMPOSIETEN IN DE FIETSTECHNIEK
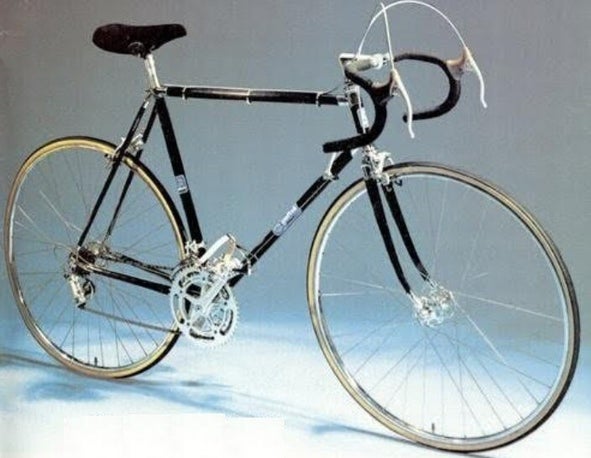
FIG.1a De Graftek G1, de eerste productie racefiets met carbon buizen (en stalen lugs ).
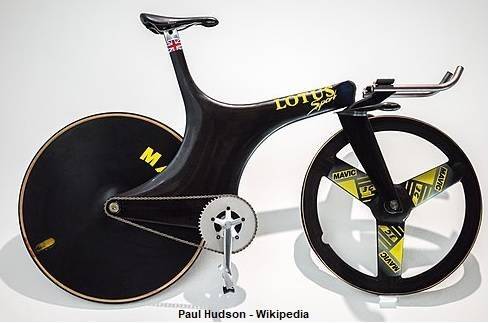
FIG.1b Een vrije vorm, uit een mal: de Lotus (inmiddels door de UCI verboden).
Een composiet bestaat uit minstens twee verschillende materialen: een matrix (moedermateriaal) en een wapening.
Voor sommige composieten kan een lichtmetalen matrix gebruikt worden. Soms gebruikt men als wapening deeltjes van SiC of Al2O3. Bij Specialized bouwde men met zulke “Metal Matrix(=M2)”- buizen van de Amerikaanse fabrikant Duralcan in de jaren negentig fietsframes. Zo’n buis wordt gemaakt door een poedermix onder hoge druk tot het smeltpunt van de laagst smeltende component te verhitten in een buisvormige mal; we zien de lichtmetalen matrix niet meer in de fietsenindustrie.
Meestal is de matrix een kunststof en de wapening een vezel. De mechanische eigenschappen van kunststoffen zijn pover vergeleken bij de wapening. Composieten van vezels en kunststoffen hebben een heel eigen plaats gekregen in de high-tech framebouw. Mensen die uit de metaal komen, hebben vaak moeite om de technische merites van vezels te beoordelen. De aanpak van het ontwerp bij constructies met composieten, vergt een specifieke benadering.
Globaal verdelen we kunststoffen in thermoharders en thermoplasten. Thermoplasten bestaan uit lange moleculen, die bij verwarming steeds makkelijker langs elkaar glijden: ze verweken. Composieten van thermoplasten worden versterkt met gehakte vezels. Het mengsel van kunststof en vezel wordt bij een temperatuur van 150 tot 250°C, in een mal gespoten tot eindproduct, b.v. kunststof wielen. De toepassing is beperkt tot industriële massafabricage. Het vezelgehalte is laag, maximaal 20 tot 30 %; de vezels zijn gewoonlijk van glas. In Taiwan maakt de firma HYC polypropyleen korrel met carbonfiber erin. Dit kan ook gebruikt worden voor 3D printen.
Thermoharders zijn kunststoffen die driedimensioneel aan elkaar “groeien”. Bij hoge temperaturen verweken ze niet, maar verkolen. Bij de meeste composieten worden thermoharders als matrix gebruikt. De wapening kan bestaan uit:
Glasvezels, worden getrokken uit gesmolten glas. Chemisch bestaat glas hoofdzakelijk uit siliciumoxide. E-glas is de meest gebruikte soort. De sterkte is redelijk, maar de elasticiteitsmodulus (= E-modulus oftewel stijfheid) is matig en de soortelijke massa hoog.
Carbonfibers, de productie hiervan geschiedt door een draad van PAN of dralon te verkolen in een oven; bij sommige vezels gebruikt men zelfs pek(teer). Dit laatste productieproces is moeilijker beheersbaar.
De verkoolde draad wordt nu verder verhit tot circa 1600°C. De koolstof gaat dan rekristalliseren tot grafiet (carbon). Het proces vreet energie, daarom is carbonfiber duur (maar sterk en stijf). Een video over het proces vinden we hier: Carbon Fiber: Conventional Carbon Fiber Conversion - YouTube
Een nieuwe toepassing van koolstof is het werken met grafeen; dit is een koolstoflaagje dat een dikte heeft van een enkele molecule! Carbon nano-buisjes zijn een andere nieuwe ontwikkeling, zie: http://mknano.com/
Aramides, als Kevlar 49 (Dupont) en Twaron HM (AKZO), zijn chemisch gelijk. Aramides hebben een hoge treksterkte en redelijke E-modulus, maar de composieten zijn slecht op druk belastbaar.
Polyetheenvezels maakt men door lange ketens PE (>10^6) op te lossen in paraffine (Spectra) of decaline (Dyneema). Ze hebben een hoge treksterkte, redelijke E-modulus en een laag gewicht. Polyetheen is een thermoplast; de eigenschappen van de composiet verslechteren snel bij temperaturen boven de 90°C.
Vectran (LCP=Liquid Cristall Polymer) is eigendom van de Amerikaanse firma Kuraray. Het is een sterke vezel, maar niet zo stijf; in veel opzichten een concurrent van de aramides. Vectran wordt onder andere gebruikt bij kunststof spaken in Spox wielen en in de duurdere banden van Continental. In banden is gebrek aan stijfheid een voordeel; alle banden zijn trouwens composieten, ook goedkope! De bandenfabrikant Vittoria brengt een band uit met grafeen; volgens de uitgelekte rolweerstanden van het lab, een grote sprong voorwaarts, maar dat zal de praktijk toch moeten uitwijzen.
Het product Magellan M5 (PIPD) verkeert nog in de ontwikkelingsfase (een Nederlandse vinding opgekocht door Dupont). Het is sterker en veel beter bestand tegen breuk dan carbon en men denkt de stijfheid nog te kunnen verbeteren. We horen er echter weinig meer over; de productieprocessen leveren problemen op en alles is militair geheim.
2.18 (Engels) Bij Colnago ( en ook bij Trek) gebruikte men in de beginjaren van het carbonframe, een buis en lug constructie, die in de oven uitgehard werd.
1.34 (Engels) Hoewel Dyneema de kwetsbaarheid van carbon sterk vermindert, wordt het weinig in de framebouw gebruikt. We zien het wel in fietskleding als valprotectie.
5.36 (Engels) Dit is tegenwoordig de meest gebruikte productiemethode voor carbon frames: weven, knippen, plakken en bakken.
20.33 (Engels)
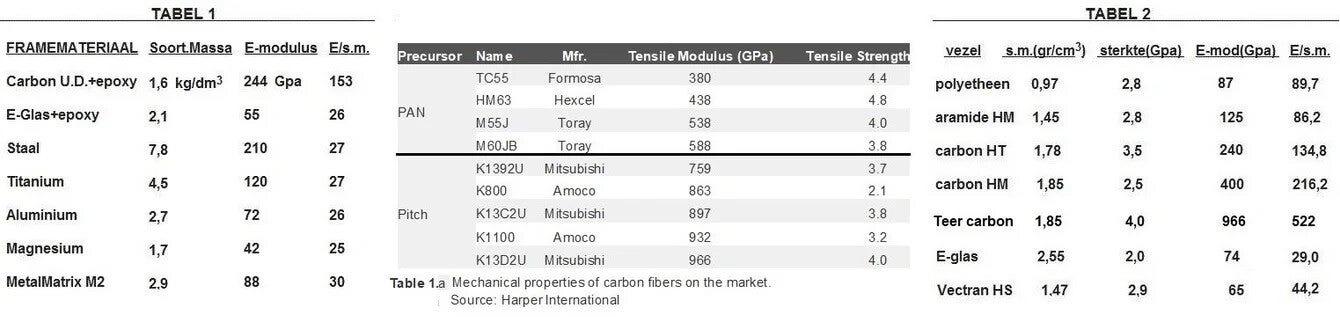
De E-modulus van de carbon composiet vermeld in TABEL 1 is alleen in de lengterichting zo stijf. Dwars op de vezel is de stijfheid veel minder. Zoals we zagen is maximaal 60% vezel en mimimaal 40% matrix (soortelijke massa 1,4). De E-modulus van de composiet zoals hij verwerkt is in de constructie, zal veel lager zijn (gewoonlijk nog geen kwart van de waarde vermeld n de tabel).
In TABEL 2 zien we een overzicht van de eigenschappen van diverse vezels. Koolstof en aramide worden geleverd in de kwaliteiten HS / HT (High Strength / High Tenacity = hoge treksterkte) en de kwaliteit HM (High Modulus= hoge E-modulus). Als constructeurs van fietsen zijn we niet zo geïnteresseerd in treksterktes. Licht en stijf is ons devies! We kiezen dus uitsluitend HM fibers. Eventueel kunnen we combinaties van carbon en aramide, of carbon en polyetheen nemen. Dit laatste weefsel is goed bestand tegen druk; een eigenschap waarin veel composieten slecht scoren en waardoor al vaak constructies faalden. De ontwerpers staren zich blind op de hoge treksterktes, terwijl constructies vaak ook op druk belast worden. De teer-carbon in tabel 2 is een topproduct van Mitsibushi ( K13D2U zie tabel 1a).
Er bestaan vele composieten met thermoharders; de meeste thermoharders worden versterkt met vulstoffen en vezels. De fabricage gebeurt vaak bij hoge temperatuur en druk, maar er zijn twee belangrijke groepen thermoharders die bij atmosferische druk en kamertemperatuur uitharden: de epoxyharsen (EP) en de onverzadigde polyesterharsen (UP= unsaturated polyester). Polyesterharsen worden vooral gebruikt in combinatie met glas of polyestervezels. Bij hoogwaardige composieten als carbon, aramide of polyetheenvezel, werkt men met epoxy; dit hecht ook goed aan metalen. De combinatie van carbonvezel en metaal kan leiden galvanische corrosie. Aanbevolen wordt metalen delen eerst met een dun laagje glasvezel of aramide te omkleden.
De grondstoffen zijn lange ketens die door toevoeging van een “harder” aan elkaar worden verknoopt. Bij epoxy gebruikt men vaak een harder die pas bij hogere temperaturen actief wordt, zo kan men het hars langer verwerken en “prepreg-weefsel” gebruiken (dit is al met hars geïmpregneerd en wordt uitgehard in een oven). Prepregs hebben een optimaal vezel-hars gehalte (60-65%). Een dergelijke vezel is wel doordrenkt met hars, maar niet glad; veel afgewerkte gladde en gelakte constructies zitten rond de 50 volumeprocent. Als we met de eenvoudige "handlay-up" bouwmethode werken, komen we meestal niet hoger dan 40% vezelgehalte. De rek voor breuk van de matrix moet groter of gelijk zijn aan die van de vezel; dat is hier vrijwel altijd het geval. Zeker voor UHM-carbon geldt dat de ultra hoge modulus de rek tot 1-1,5% doet afnemen; dit is bros te noemen. Het samenspel tussen matrix en vezel is kritisch. De matrix dient de vezel geheel te doordrenken en zich goed aan de vezel te hechten. De matrix verdeelt de belasting over de vezels (trek en druk). Bovendien beschermt het hars de vezels tegen chemische en mechanische invloeden. Aan het eind van de vezel, geeft het hars de krachten door aan de omringende vezels. Polyetheenvezels krijgen een corona-behandeling (vonkenboog) om de hechting tussen vezel en matrix te bevorderen. Een groot probleem zijn de verschillen in uitzettingscoëfficiënt van matrix en vezel. Als de vezels zich losgewerkt hebben, nemen ze geen krachten meer op (vergelijkbaar met een losse spaak). Er ontstaat dan een zwakke plek in de composiet, waarvan niets te zien is, en die aanleiding kan zijn tot een plotselinge breuk (geen rek!).
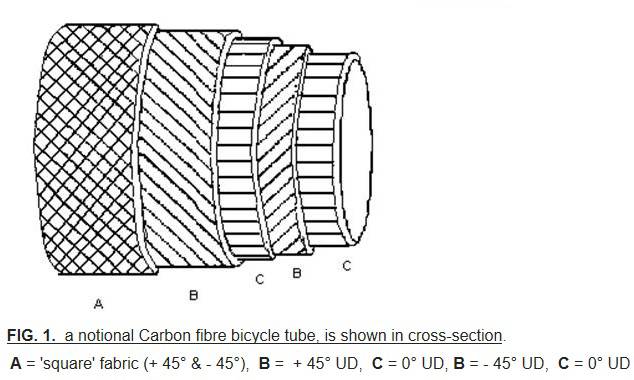
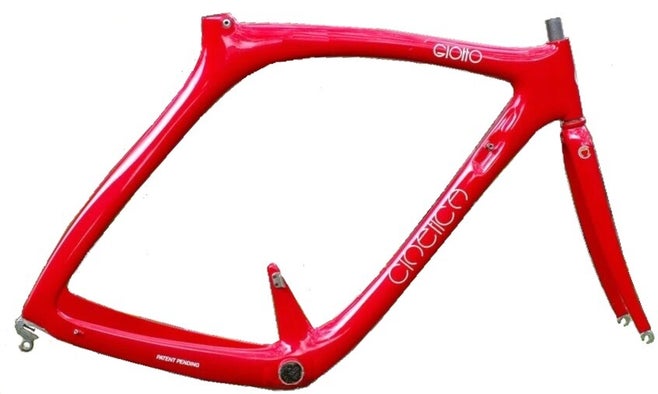
FIG.1c Vrije vorm bij deze carbon monocoque uit 1989 : de Cinetica Giotto
De diameter van de afzonderlijke draadjes (filamenten) is ± 0,007mm. Bundels filamenten heten rovings; men kan deze rovings tot weefsel verwerken (rovingmatten). Fijn weefsel bevat ongeveer 1000 (1 K) filamenten per streng; in de framebouw wordt ook wel grover weefsel gebruikt tot 3K. In de botenbouw zelfs 24K en meer....
Weefsel met vrijwel alle draden in een richting noemt men Uni Directoraal (U.D.); dit wordt gebruikt om de stijfheid in een bepaald vlak te verbeteren. In een frame waar veel verschillende belastingen op komen, kan daarom ook “vierkant” weefsel verwerkt worden, hier zijn de schering en inslag gelijk. Dit is de buitenlaag in FIG.1; de stijfheid van vierkant weefsel (A) is hooguit een kwart van U.D. in de lengterichting (C), maar wel in alle richtingen ongeveer gelijk. Het is ook mogelijk enkele lagen U.D. onder verschillende hoeken (B) te verwerken. Juist uit het oogpunt van optimalisatie, zien we dat de moderne bouwers niet enkele dikke lagen, maar veel dunne lagen verwerken. De matrix mag niet op afschuiving belast worden. Dit houdt in dat bij een buis-lug-frame de vezels van de buis de lugs onder een hoek van 45° moeten ingaan. Dwars op de vezels (90 en 0°) draagt de matrix deze krachten (dat niet gaat lang goed!). Bij veel frames is de buitenste laag een afwerklaag en niet echt noodzakelijk voor de sterkte. Dit maakt de buis minder gevoelig voor krassen.
Een eenvoudige constructiemethode is de handvorm of “handlay-up” methode. Men werkt hierbij met een simpele mal van hout of gips. De oppervlakte ervan wordt bestreken met een lossingmiddel, gewoonlijk polyvinylalcohol (PVA), omdat dit oplosbaar is in water. Hierop brengt men een dunne laag hars aan, waarop de rovingmatten of weefsels gelegd worden. De mat wordt goed aangedrukt om de weefsels te doordringen met hars en luchtbellen te verwijderen. Nu wordt op het weefsel weer een nieuwe laag hars aangebracht, en eventueel weer een nieuwe laag weefsel.
Door aan de buitenkant vacuüm te zuigen, kan men luchtbellen vermijden en overtollig harsgebruik voorkomen. Dit is een methode die veel gebruikt wordt bij stroomlijnen. Meestal zijn er twee mallen: een linkse en een rechtse of een onderste en een bovenste. Het uitharden van de hars kan bij kamer-temperatuur, maar vaak gebeurt het in een oven; hier verloopt de uitharding sneller en verbetert de sterkte van het hars.
Als men met een kern, "wood-core" methode, van PUR-schuim of balsahout werkt, blijft deze zitten. Dit is extra gewicht (en stijfheid).
Optimalisatie van een fietsframe kan alleen als we met dunne rovingmatjes werken! De prijs van dunne matten is bijna even hoog als die van dikkere matten. Het is duurder en veel meer werk om al die dunne laagjes op elkaar te plakken. De meest hoogwaardige racefietsframes worden in een mal gemaakt, en als een geheel (monocoque) uitgehard in een oven. Zo krijgen we de optimale verhouding gewicht/stijfheid. Men brengt aan de binnenkant van het frame een ballon (airbag) aan, om het overtollige hars naar buiten te drukken. Hierdoor kan men het maximaal haalbaar vezel percentage van 60% bereiken. Bij goedkopere carbonframes kiest men voor overdimensionering door dikkere lagen te nemen (minder werk). Uitgaande van het feit, dat de eindsterkte op de gevoelige punten gelijk is (sterk genoeg), neemt het gewicht toe, omdat ook de laag belaste framedelen dik zijn uitgevoerd. Het verschil in dure en goedkopere carbon frames is dan ook niet alleen het kwaliteitsverschil in het carbon, maar de kwaliteit van de productie-methode. Bij goedkope frames zal de airbag en het PUR-schuim blijven zitten; bij dure frames zal men deze verwijderen.
Er zijn fabrikanten die echt al het lamineerwerk zelf uitvoeren, vanaf de carbonmatten tot het complete frame; hier is het knippen en plakken, mallen vullen en uitharden. Bij veel framebouwers zijn de constructies al ver voorbewerkt bij aanschaf. De fabrikant Columbus maakt bij voorbeeld zulke bouwpakketten. De voor- en achtervorken komen kant en klaar uit de fabriek, de buizen ook. Het geheel hoeft nog maar samengesteld te worden, maar de variatie is erg beperkt.
In Taiwan maakt de firma HYC een Polypropeen korrel met carbonfiber erin, die via extrusie en spuitgieten verwerkt kan worden. Als de sterkte en gewicht niet te veel afwijken, een zeer veel belovende toepassing. Hierbij is het frame ook nog recyclebaar. De productie is dan vergelijkbaar met de Columbus frames.
Informatie via boeken en Internet over werken met composieten
Het meest gebruikte boek over composieten : Gerard Lok c.s.: Praktijkhandboek Kunststoffen ISBN 90 6410 353 4 .
Dit boek, en veel gebruikte composietmaterialen als epoxy en carbon, zijn via postorder verkrijgbaar bij: www.polyservice.nl
Op de Amerikaanse ligfietssite WISIL is heel veel te vinden over zelfbouw in composieten.
Uiteraard ook veel composieten bij zelfbouwers op de site van de NVHPV : www.ligfiets.net
Nog wat leveranciers: http://www.polyestershoppen.nl , https://www.easycomposites.eu/ , en voor speciale materialen: http://specmaterials.com/index.htm
Time fietsen: al 50 jaar groot in Composieten!
Ook een composiet: http://www.instructables.com/id/How-to-Build-a-Bamboo-Bicycle/
De theorie van composieten
In de moderne werktuigbouw kan men met de computer via 3D “eindige elementen analyses (FEA)”, de belastingen op het ontwerp demonstreren. Als die bekend zijn, gaan we optimaliseren. De zwaarst belaste punten worden versterkt en men haalt materiaal weg op de plekken met een lagere belasting. Sommige programma's geven de berekende resultaten in fraaie kleurplaten weer (zie FIG.2b). Er zijn in de loop der tijd ook wel eenvoudigere freeware-programma's geweest, maar natuurlijk met een beperkte functionaliteit en toepassing . Het boek "Composieten" (HBO-niveau) is een gratis uitgave.
Vezels zijn alleen in de lengterichting erg stijf, dwars op de vezel is de stijfheid veel minder. We verwerken de vezel in allerlei richtingen (zie FIG.1), om te voorkomen dat het frame in een bepaalde richting te slap wordt. In dit geval krijgen we een gemiddelde waarde van 60Gpa, veel minder dan 244Gpa, maar altijd nog ruim 2 maal zo stijf als staal bij de zelfde diameter en massa.
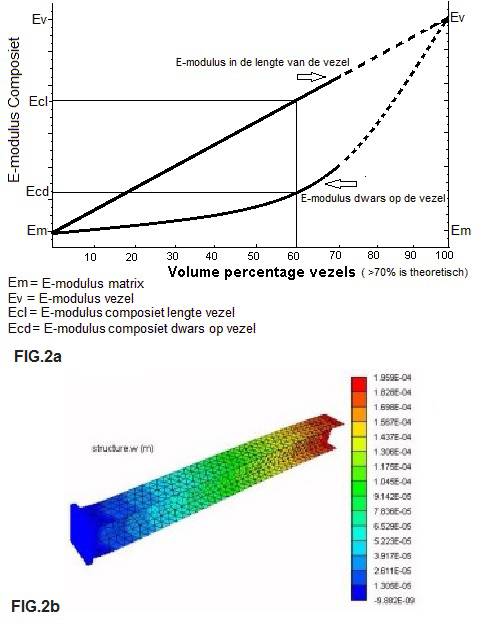
De E-modulus van epoxy ligt tussen de 2 (lijm) - 20Gpa (plaatmateriaal); voor composieten ongeveer 4 Gpa. Zoals we zagen is maximaal 60% vezel (de E-modulus van carbon-HM = 400Gpa) en mimimaal 40% matrix. In de lengte is de stijfheid: E composiet= (E vezel) * ( Vol% vezel) + (E matrix) * ( Vol% matrix) , bij voorbeeld: E composiet= 400 * 60/100 + 4 * 40/100 = 242Gpa.
Dwars op de vezel is dat: E composiet= (E vezel * E matrix) / (E vezel * Vol% matrix + E matrix * Vol% vezel) = 400 * 4 / (400 * 40/100 + 4 * 60/100) = 10Gpa. Deze berekening geeft een valkuil aan, voor ontwerpers van composietconstructies.
Er is er nog zo een: de belasting op druk. Dit geldt zeker voor een U.D.-weefsel. Denk eens even na; je neemt een bosje touwtjes en plakt die met een flinke klodder lijm aan elkaar. Als we aan deze composiet trekken, hebben we een sterk object; als we hierop duwen, stort de zaak gauw in. De touwtjes kunnen geen druk opnemen; de lijm (matrix) moet de druk dragen en de constructie wordt op afschuiving van de matrix belast. Druk wordt aangeduid met de Griekse letter σ (sigma)
σ composiet = G matrix * (1- Vol % fibers )
We komen nu bij een materiaaleigenschap, die schuifmodulus of glijdingsmodulus genoemd wordt: G.
Een belangrijke variabele in de berekening van G is de dwarscontractie-coëfficiënt of Poisson-factor, hieronder aangegeven met de Griekse letter ν (nu); voor epoxy circa 0,3.
G = E : (2 . (1 + ν ))
Informatie over de theorie van composieten:
Een computerprogramma als hulp voor het ontwerpen van laminaatconstructies (freeware):
https://tu-dresden.de/ing/maschinenwesen/ilr/lft/elamx2/elamx?set_language=en
Een FEA programma: https://academy.3ds.com/en/software/abaqus-student-edition
Een handboek in het Duits en het Engels: http://ezentrumbilder3.de/rg/pdf/Handbuch_deutsch.pdf .
Over composieten (Engels): http://www.princeton.edu/~maelabs/hpt/materials/composites.htm